機械結構分析的問題,我們搜遍了碩博士論文和台灣出版的書籍,推薦LudwigvonMises寫的 人的行為:經濟學專論(上)(4版) 和的 從零開始學機械控制(原著第2版)都 可以從中找到所需的評價。
另外網站簡單機器人的結構設計- 維基學院,自由的研習社群也說明:1.2 自由度; 1.3 輪式機器人的平面運動; 1.4 機械臂的空間運動. 2 機器人結構. 2.1 從大腦到肢體:機器人系統; 2.2 骨骼:機構; 2.3 肌肉:制動器 ...
這兩本書分別來自五南 和化學工業出版社所出版 。
國立彰化師範大學 工業教育與技術學系 盧建余所指導 林裕傑的 開發PCB複合式板植針治具之自動化線針植針機 (2021),提出機械結構分析關鍵因素是什麼,來自於PCB電性測試、工業相機CCD、PID控制。
而第二篇論文國立中央大學 機械工程學系 林錦德所指導 魏子凱的 結合遺傳演算法與類神經網路之 分散式機械結構最佳化系統之研究 (2020),提出因為有 結構最佳化設計、遺傳演算法、類神經網路、分散式運算系統的重點而找出了 機械結構分析的解答。
最後網站1102_機械結構振動學(R2ME000031A) - 數位學習M園區則補充:英文名稱: Vibration of Mechanical Structure ; 授課目的: 對於機械工程而言,與振動相關的知識是很重要的。學生在修習本課程後,應可以理論分析、數值模擬、或實驗 ...
人的行為:經濟學專論(上)(4版)
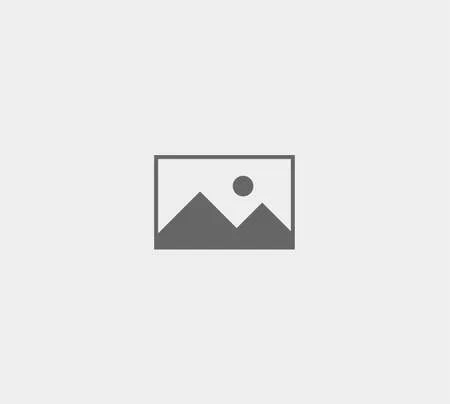
為了解決機械結構分析 的問題,作者LudwigvonMises 這樣論述:
中華經濟研究院特約研究員 吳惠林 專文導讀 當今大多數大學裡,以經濟學為名所傳授的東西,實際上是在否定經濟學。 米塞斯——繼亞當·史密斯之後,最重要的經濟學家,其代表作《人的行為》被譽為意義最深遠的經濟學著作。他把經濟學納入社會哲學或行為通論的架構中來處理,與當代主流經濟學者所宗奉的凱因斯,把經濟學寄託於數學或統計學部門有所不同。這一差異,關乎他們個人學問造詣之深淺廣狹者,乃至關乎經濟學是否被確實了解者,其事小;關乎其影響於人類文明演化之分歧者,其事大。 經濟學絕不該遭到降格,關在教室和統計室裡,也絕不該留在少數人的圈子裡祕傳。它是人生和行為的哲學,關
係到每個人和每件事情。它是文明,和人之所以為人,必不可少的精髓。在此提到這個事實,並非在老王賣瓜、自賣自誇。今天把這個突出地位分派給經濟學的,不是經濟學家,而是所有的人們。 所有當今的政治議題,都涉及一般稱之為經濟問題的問題。在當前關於社會和政治事務的討論中,所有爭執都涉及行為學和經濟學的根本問題。每個人心裡都盤據著某些經濟學說。 和從前以為是哲學和神學研究主題的那些問題相比,哲學家和神學家現在對於經濟問題更感興趣。小說和戲劇現在也從某些經濟理論的角度處理所有人間世事,包括兩性關係。每個人都想到經濟學,不管他本人知不知道經濟學。在加入某個政黨時,以及在投下他的選票時,每位公民都必然
連帶地採取某個立場,看待一些基本的經濟理論。 (本書為上冊,收錄前17章,第18章至第39章收錄於下冊)
機械結構分析進入發燒排行的影片
幹機加工最怕的除了人身安全問題,再就是機械故障了,其中最讓人心顫的自然是撞機、崩刀。。。有經驗的大佬都懂這種感覺。那麽怎麽避免這兩個致命點呢?
刀具崩刃的原因及對策
1)刀片牌號、規格選擇不當,如刀片的厚度太薄或粗加工時選用了太硬太脆的牌號。
對策:增大刀片厚度或將刀片立裝,選用抗彎強度及韌性較高的牌號。
2)刀具幾何參數選擇不當(如前後角過大等)。
對策:可從以下幾方面著手重新設計刀具。 適當減小前、後角。 采用較大的負刃傾角。 減小主偏角。 采用較大的負倒棱或刃口圓弧。 修磨過渡切削刃,增強刀尖。
3)刀片的焊接工藝不正確,造成焊接應力過大或焊接裂縫。
對策:避免采用三面封閉的刀片槽結構。正確選用焊料。避免采用氧炔焰加熱焊接,並且在焊接後應保溫,以消除內應力。盡可能改用機械夾固的結構
4)刃磨方法不當,造成磨削應力及磨削裂紋;對PCBN銑刀刃磨後刀齒的振擺過大,使個別刀齒負荷過重,也會造成打刀。
對策:采用間斷磨削或金剛石砂輪磨削。選用較軟的砂輪,並經常修整保持砂輪鋒利。註意刃磨質量,嚴格控制銑刀刀齒的振擺量。
5)切削用量選擇不合理,如用量過大,便機床悶車;斷續切削時,切削速度過高,進給量過大,毛坯余量不均勻時,切削深度過小;切削高錳鋼等加工硬化傾向大的材料時,進給量過小等。
對策:重新選擇切削用量。
6)機械夾固式刀具的刀槽底面不平整或刀片伸出過長等結構上的原因。
7)刀具磨損過度。
對策:及時換刀或更換切削刃。
8)切削液流量不足或加註方法不正確,造成刀片驟熱而裂損。
對策: 加大切削液的流量。 合理布置切削液噴嘴的位置。 采用有效的冷卻方法如噴霧冷卻等提高冷卻效果。 采用*切削減小對刀片的沖擊。
9)刀具安裝不正確,如:切斷車刀安裝過高或過低;端面銑刀采用了不對稱順銑等。
對策:重新安裝刀具。
10)工藝系統剛性太差,造成切削振動過大。
對策: 增加工件的輔助支承,提高工件裝夾剛性。 減小刀具的懸伸長度。 適當減小刀具的後角。 采用其它的消振措施。
11)操作不慎,如:刀具由工件中間切入時,動作過猛;尚未退刀,即行停車。
對策:註意操作方法。
撞機的原因歸納起來大概有9點
1)程序編寫錯誤。
工藝安排錯誤,工序承接關系考慮不周詳,參數設定錯誤。
A. 坐標設定為底為零,而實際中卻以頂為0;
B. 安全高度過低,導致刀具不能完全擡出工件;
C. 二次開粗余量比前壹把刀少;
D. 程序寫完之後應對程序之路徑進行分析檢查。
2)程序單備註錯誤。
A.單邊碰數寫成四邊分中;
B.臺鉗夾持距離或工件凸出距離標註錯誤;
C.刀具伸出長度備註不詳或錯誤時導致撞刀;
D.程序單應盡量詳細;
E.程序單設變時應采用以新換舊之原則:將舊的程序單消毀。
3)刀具測量錯誤。
A.對刀數據輸入未考慮對刀桿;
B.刀具裝刀過短;
C.刀具測量要使用科學的方法,盡可能用較精確的儀器;
D.裝刀長度要比實際深度長出2~5mm。
4)程序傳輸錯誤。
A.程序號呼叫錯誤或程序有修改,但仍然用舊的程序進行加工;
B.現場加工者必須在加工前檢查程序的詳細數據;
例如程序編寫的時間和日期,並用熊族模擬。
5)選刀錯誤。
6)毛坯超出預期,毛坯過大與程序設定之毛坯不相符。
7)工件材料本身有缺陷或硬度過高。
8)裝夾因素,墊塊幹涉而程序中未考慮。
9)機床故障,突然斷電,雷擊導致撞刀等。
CNC加工中心數控機床作為高精度的機床,防撞是非常必要的,要求操作者養成認真細心謹慎的習慣,按正確的方法操作機床,減少機床撞刀現象發生
開發PCB複合式板植針治具之自動化線針植針機
為了解決機械結構分析 的問題,作者林裕傑 這樣論述:
摘要本論文旨在開發PCB複合式板植針治具之自動化線針植針機應用於PCB電性測試上。本機台分為硬體機台開發與軟體控制系統設計,機台以鋁擠底座上放置XY平台,並於XY平台上方設置兩個A、B傾斜測試平台及工業相機CCD (Charge Coupled Device),其中工業相機主要監控避免人為疏失及觀測植針座標。軟體開發為讀取原始鑽孔之植針圖檔,經過轉換成可編輯之座標檔匯入樹梅派作業系統OS (Operating System)下使用Python程式語言讀取植針機台原點為絕對座標點,再將植針之點與絕對座標點進行路徑規劃後,接著PID控制器驅動X、Y、A及B 4軸馬達至目標點,最後讀取4軸馬達編碼
器反饋的位置數據即為目標座標再進行位置微調補償後,確定目標點,再執行探針植入治具,直到此治具完成植針,再進行此治具下一程序的電性測試。 本研究的優點是藉由自動化機台協助人力,確認探針精準植入植針治具中,使PCB電性測試時流程減少不良率,提升工作效率實現自動化生產。
從零開始學機械控制(原著第2版)

為了解決機械結構分析 的問題,作者 這樣論述:
該書從機械工程控制的基礎理論入手,通過圖解的形式,描述了拉普拉斯變換、典型環節傳遞函數的分析方法、反饋控制、控制系統的結構圖、瞬態響應、頻率響應等。該書理念先進,形式活潑,圖文並茂,通俗易懂。書中每個知識點後面都設有例題,並給出了題目分析和解答的詳細步驟,易於理解。每章后還附有習題,書後有習題解答,可供讀者鞏固學習和參考之用。本書適合普通本科非機械類、高職機械類專業的學生閱讀,也適合對相關知識感興趣的自學者閱讀。
結合遺傳演算法與類神經網路之 分散式機械結構最佳化系統之研究
為了解決機械結構分析 的問題,作者魏子凱 這樣論述:
本文整合結構最佳化方法及分散式運算系統,建立一機械結構最佳化系統。其系統突破以往於單一機台執行最佳化分析的模式,藉由運算資源的整合,加速最佳化方法的計算,達至提升資產使用率及降低產品開發時間成本之兩大目的。於結構最佳化方法上,結合至遺傳演算法及類神經網路模型,使最佳化方法擁有全域搜尋之能力,且能透過基於自適性規則的類神經網路模型,在模型運算準確度達至標準的條件下,取代原適應度評估方式,提升演算法的運算效率。在分散式運算系統上,使用聯網技術整合場域內的運算資源,建立一客戶端/伺服端的系統架構,當客戶端執行最佳化分析後,伺服端能夠將尚未分析的變數任務分配予閒置的資源,並可將設計變數及分析結果儲存
於資料庫中,該系統能夠大幅度地降低最佳化分析的所需時間且擁有數據管理的能力。接著,本研究將提出結合遺傳演算法及類神經網路模型的分散式機械結構最佳化系統應用於非凸優化函數及數個結構最佳化分析案例上,進行系統的實作及驗證。由結構最佳化案例的結果可得,本文提出之結構最佳化系統相較於其他的最佳化方法能夠大幅度縮短最佳化分析的時間,且獲得較佳的分析結果,驗證至該機械結構最佳化系統之實用性。
機械結構分析的網路口碑排行榜
-
#1.机械结构分析与设计- 快懂百科 - 头条百科
《机械结构分析与设计》是由北京理工大学出版社与2009年08月01日出版的一本机械行业书籍,作者李小红,韦林。 於 www.baike.com -
#2.Ansys 結構的價格推薦- 2022年6月| 比價比個夠BigGo
7269.ANSYS Workbench 19.0結構分析從入門到精通(簡體書) 北京兆迪科技有限公司編著 ... 基於ANSYS的機械結構有限元分析實訓教程. bigcoin white 2.4%. 於 biggo.com.tw -
#3.簡單機器人的結構設計- 維基學院,自由的研習社群
1.2 自由度; 1.3 輪式機器人的平面運動; 1.4 機械臂的空間運動. 2 機器人結構. 2.1 從大腦到肢體:機器人系統; 2.2 骨骼:機構; 2.3 肌肉:制動器 ... 於 zh.m.wikiversity.org -
#4.1102_機械結構振動學(R2ME000031A) - 數位學習M園區
英文名稱: Vibration of Mechanical Structure ; 授課目的: 對於機械工程而言,與振動相關的知識是很重要的。學生在修習本課程後,應可以理論分析、數值模擬、或實驗 ... 於 euni.niu.edu.tw -
#5.樂高機械結構設計| 天瓏網路書店
書名:樂高機械結構設計,ISBN:7302583986,作者:程罡,出版社:清華大學,出版日期:2021-06-01, ... USB 應用分析精粹:從設備硬件、固件到主機端程序設計 ... 於 www.tenlong.com.tw -
#6.机械结构产品设计的方法分析 - 公务员期刊网
机械结构 产品设计的方法分析摘要: 【内容摘要】文章通过研究经典机械结构对产品设计的指导作用,提出一种高效合理的产品设计方法。该方法从研究经典产品在功能模块上 ... 於 www.21ks.net -
#7.產業新尖兵*全額補助】智慧製造-機構設計與結構分析技術師 ...
【產業新尖兵*全額補助】智慧製造-機構設計與結構分析技術師養成班(職業)(資訊): ☆模組一:智慧設計 單元 時數 1.機械製圖基礎與實務...;培養第二專長、充實自己的 ... 於 www.1111edu.com.tw -
#8.結構分析- 維基百科,自由的百科全書
在土木工程範圍內,重要的的結構包含建築,橋樑和塔;在其他工程分支中,結構可以包含但不僅限於,船舶和飛機的框架,蓄水池,壓力容器,機械系統,和電力系統支架。工程師 ... 於 zh.wikipedia.org -
#9.機械結構分析-新人首單立減十元-2022年6月 - 淘寶
當然來淘寶海外,淘寶當前有1605件機械結構分析相關的商品在售。 ... CATIA有限元工程結構分析CAE第2版有限元分析基礎工程實例機械工業出版社工業技術機械工程正版 ... 於 world.taobao.com -
#10.【研討會講義】9/23 Ansys 結構振動應用技術研討會
本次研討會邀請專家和教授針對旋轉機械、電子產品與封裝製程等領域,分享其應用的經驗,期望讓與會者更加了解Ansys Mechanical在結構領域的強大分析 ... 於 www.cybernet-ap.com.tw -
#11.机械结构动态设计及应用分析.pdf_文档分享网
城市建筑1研究探讨I URBANISM AND ARCHITECTURE RESEARCH DIS CUSSION机械结构动态设计及应用分析沈新铭胡月明摘要随着社会科技的不断创新发展, ... 於 m.wdfxw.net -
#12.机械结构可靠性设计方法_检测资讯
进行结构可靠性分析主要涉及3个问题:1)确定影响应力、强度的基本随机变量;2)根据产品的故障模式和故障机理模型,建立功能函数;3)采用结构可靠度 ... 於 m.anytesting.com -
#13.机械结构创新设计的分析
摘要:在介绍应用变元法进行机械结构的创新设计原理后,指出设计时应遵循的8项准则。针对石油与石化设备易于腐蚀的弱点,着重阐述了结构的防腐蚀设. 於 m.xzbu.com -
#14.機械結構設計過程中應重點考慮哪些方面? - 小蜜蜂問答
對承載零部件的結構進行載荷分析,必要時計算其承載強度、剛度、耐磨性等內容。並透過完善結構使結構更加合理地承受載荷、提高承載能力及工作精度。同時 ... 於 beesask.com -
#15.機械結構設計-第2版 - 讀冊
本書綜合了機械專業《結構力學》和《金屬結構》的主要內容,並且把兩者有機融合 ... 所附“機械結構設計上機教材”光碟詳細敘述了應用ANSYS程式進行結構有限元分析的入門 ... 於 www.taaze.tw -
#16.基本原理
一) 在機械設計上實際進行應力分析時,我們發現機械設計之基本公式並 ... 在機械設計之結構分析上,有限元素分析係將一結構分成許多微小單. 於 www.wunan.com.tw -
#17.AutoCAD 實體模型之公差標註與分析自動化系統
公差與受力對機械結構變形影響之探討. A study on The Effect of Tolerances and Forces on deformation of Mechanism. 研究生:何益君 指導教授:蔡志成. 於 www.me.nchu.edu.tw -
#18.士盟科技CAE結構分析|CST高頻模擬分析,提供技術支援與工程 ...
業務遍及世界各地,覆蓋廣泛的工程領域:航空航太、國防軍事、能源電力、核工業、石油化工、船舶與海洋工程、工程機械、結構和土木工程等。 於 simutech.com.tw -
#19.基于Solidworks的自动装卸机械结构设计及分析 - 汉斯出版社
本文以抓取普通纸箱为工作背景,利用Solidworks软件进行建模和运动仿真,对桁架结构的自动装卸机械系统结构进行设计及零部件的选用,利用ANSYS进行力学分析,对设计结果 ... 於 www.hanspub.org -
#20.機械結構設計與維護:內容簡介,圖書目錄 - 中文百科全書
《機械結構設計與維護》是2013年9月1日化學工業出版社出版的圖書,作者是高朝祥。 ... 機構的組成及其運動分析、平面連桿機構、凸輪機構、間歇運動機構、機械連線、撓 ... 於 www.newton.com.tw -
#21.《机械结构分析与设计实践教程》【摘要书评试读】- 京东图书
京东JD.COM图书频道为您提供《机械结构分析与设计实践教程》在线选购,本书作者:韦林,林泉,出版社:北京理工大学出版社。买图书,到京东。网购图书,享受最低优惠 ... 於 item.jd.com -
#22.2.02.1 机械原理:机构的结构分析——高副低代.(新课程)
视频课程完全免费,请大家记得三连哦: 1、关注微信公众号: 机械 研帮,获取课件; 2、B站旧版视频在 ... 2.02.1 机械 原理:机构的 结构分析 ——高副低代. 於 www.bilibili.com -
#23.机械结构系统的定义,机械结构分析_博鱼·体育(中国)官网
... 机械结构分析;步兵机器人的作用;机械结构工程师;机械结构系统的定义什么是 ... 机械结构系统的最新报道-其零部件通常可分为:光学系统、机械类、电气类、机电 ... 於 www.kasgo.cn -
#24.機械結構分析與設計 - 中文百科知識
作者: 一般工業技術《21世紀全國高等教育套用型精品課規劃教材:機械結構分析與設計》是根據高等院校機械類專業教學改革實踐,對傳統的力學和機械設計基礎教材進行 ... 於 www.easyatm.com.tw -
#25.機車車體結構分析與最佳化設計之研究卓進興
本文主要研究機車結構在設計的過程中,如何利用電腦模擬分析的技術,來預知其結構上 ... [2] 趙士偉,機車結構減振之設計方法,碩士論文,國立台灣大學機械所,2000。 於 people.dyu.edu.tw -
#26.机械结构热-力问题的不确定性分析方法研究
机械结构 热-力问题的不确定性分析方法研究. 汪兵. [摘要]:考虑到机械结构所处环境,制造误差,部分参数之间存在相关性等因素的影响,像材料参数,几何参数之类的重要参数间 ... 於 cdmd.cnki.com.cn -
#27.三維微電子機械系統結構分析與設計 - 海词词典
三維微電子機械系統結構分析與設計的英文翻譯. 基本釋義. Analysis and Design of the Architecture in 3D MEMS. 三維微電子機械系統結構分析與設計的相關資料:. 於 dict.cn -
#28.結構及機械設計分析實驗室
結構 及機械設計分析實驗室. ▫ 金屬材料動態應變量測. 認可項目. 認證範圍. 金屬材料動態應變量測. 應變範圍:±2%. 環境溫度:-75℃~175℃. 頻寬範圍:≤1 kHz. 於 www.ncsist.org.tw -
#29.93 Co-op | 機械工程系 - 南臺科技大學
1. 張超群. 編寫與交通事故鑑定有關之力學參考. 交通部/國立成功大學. 450,000 · 2. 呂金塗. 機械結構分析合作案第二期. 東捷科技股份有限公司. 200,000 · 3. 王聖璋. 奈米碳 ... 於 mech.stust.edu.tw -
#30.Solidworks機械設計與結構分析實務班- 夏季學習課程 - 逢甲大學
本課程以電腦輔助機械設計為核心,培養創意設計、工程圖繪製、零件建模繪圖能力,並導入結構分析實務操作,使學員能順利投入機械產業。 於 www.fcu.edu.tw -
#31.ANSYS結構分析技術師 - ivendor科技聯盟
ANSYS多目標最佳化課程可以提供學員在從事精密機械、智慧機具、土木設計時的一個最佳化設計工具,結合結構分析與最佳化設計希望有助學員建立更精確的設計方法與提昇 ... 於 www.ivendor.com.tw -
#32.經濟部主辦-2015年機械結構分析應用技術研討會 - 虎門科技
根據GTAP(Global Trade Analysis Project)模型之分析,不管台灣是否洽簽ECFA,中韓FTA均將對台灣產業造成負面衝擊,尤以塑化業、機械業及紡織業受創 ... 於 com.cadmen.com.tw -
#33.结构分析法(设计) - MBA智库百科
结构分析 法是产品的结构是指产品内部结构、机械机构诸要素的排列组合方式进行分析的一种方法。同样一些要素,排列组合的方式不同,就可能具有完全不同的性质、特征与 ... 於 wiki.mbalib.com -
#34.鋼結構設計、結構分析書在PTT/mobile01評價與討論
在機械結構分析這個討論中,有超過5篇Ptt貼文,作者MEQQQ也提到各位大大好小弟四中機械“學士” 一年半傳產機構經驗英文還可以想轉到消費性電子機構目標是前進外商品牌廠 ... 於 camping.reviewiki.com -
#35.歷屆試題- 郵政人員升資考試 - 鼎文公職
99, 佐級晉員級, 技術類(選試機械原理概要), 郵政法規概要. 99, 員級晉高員級, 業務類, 民法 ... 99, 員級晉高員級, 技術類(選試資訊系統與分析), 工程經濟. 於 m.ting-wen.com -
#36.機械結構設計機械設計-結構與電腦輔助設計_徐業良_Unit
結構分析 法是產品的結構是指產品內部結構,機械機構諸要素的排列組合方式進行分析的一種方法。同樣一些要素,排列組合的方式不同,就可能具有完全不同的性質,特征與功能。 於 www.beliukk.co -
#37.工具機機械設計工程師能力鑑定說明-結構篇
工具機機械設計工程師能力鑑定說明結構篇 ... 等等,因此如何將學校所學與工具機相關原理進行對應, 可透過CNC工具機機械人才鑑定進行盤點與分析。 於 www.maonline.com.tw -
#38.机械结构设计工程师需要什么样的分析软件? - 网易
机械结构 设计工程师需要什么样的分析软件?,autocad,matlab,机械,软件包,工程师. 於 www.163.com -
#39.第一章緒言Introduction - 1-1 機構與機器的定義
這個組合稱為機構(Mechanism),如變形機器人玩具、機械式鐘錶、…等。 ... 每一個機構與機器都有一個結構件,稱為機架(Frame),是由一個或數個機件. 於 sparc.nfu.edu.tw -
#40.Jerry的機械論壇- 【學會結構分析的好處】 當你學會了『機構 ...
【學會 結構分析 的好處】 當你學會了『機構 分析 』 在設計上能夠更放心地去開發,因為『機構 分析 』,一方面能提前確定可行性,另一方面可以更精簡化你 ... 於 hi-in.facebook.com -
#41.基于等几何的快速CAD/CAE一体化机械结构设计和不确定分析 ...
数值模拟技术已成为机械结构设计、分析和优化不可或缺的工具,并广泛应用于汽车船舶,航空航天等各个领域。受限于传统数值模拟中CAD和CAE之间的鸿沟和反复计算修改模型所 ... 於 wap.cnki.net -
#42.机械结构设计与分析 - 振国范文网
机械结构 设计与分析. 字号:大 中 小. 摘要:机械结构设计具体是指机械工程师完成机械产品构思之后,按照设计方案的要求,再进行机械工程图纸的绘制,并且将设计思路 ... 於 www.zzzhenguo.com -
#43.机械结构设计基本知识- 头条搜索
分享图解机械结构设计要点分析及应用实例手册,教你不再走弯路 · 本书结合机械设计的知识和方法,分析了机械结构的设计要点。 图解的机械结构主要包括螺纹连接, ... 於 m.toutiao.com -
#44.機械/工具機CAE 技術研討會
本技術研討會,將特別針對機械/工具機產業的設計/研發需求,介紹新一代的CAE ... 電腦輔助工程分析(CAE) 工具早已被廣泛應用,利用電腦分析模擬實際物理問題,例如結構 ... 於 www.terasoft.com.tw -
#45.【機器人學】當前工業機器人應用中的機械結構設計方法分析
【機器人學】當前工業機器人應用中的機械結構設計方法分析. 原創 gpeng832 2019-04-04 18:49. 作者:鄭會翔 摘要: 工業機器人是智能化的製造設備,對工業生產效率的 ... 於 www.twblogs.net -
#46.楊銘安- 振動衝擊與結構分析工程師- 廣達電腦 - LinkedIn
我是楊銘安,畢業於國立台灣科技大學機械工程研究所,目前就職於廣達電腦擔任雲端應用伺服器振動衝擊與結構分析工程師。 大學時期的系上名次皆維持在前10%,在求學期間 ... 於 tw.linkedin.com -
#47.應用CAE軟體於結構振動分析 - 車輛工程系
國立屏東科技大學研發長、工學院院長、推廣教育中心主任、機械工程系系主任 專長:有限元素分析、振動與噪音分析檢測與防制、車輛動力學、智慧型材料結構系統應用 於 ve.ntut.edu.tw -
#48.快速、簡單建模建築、機械等結構分析與設計系統軟體 - 每日頭條
有限元分析軟體RFEM 是由Dlubal 公司開發的建築、機械等領域通用的空間有限元結構分析與設計系統的基礎軟體。 於 kknews.cc -
#49.機械設計工程師職能基準
K133 冷凍空調基本原理. T3 符合客. 戶需求完. 成機械系. 統整合之. 設計. T3.1 善用工程分析工. 具. T3.2 功能及可行性分. 析. T3.3 單元與結構整合. 於 icap.wda.gov.tw -
#50.机械结构分析与设计实践教程[韦林编] pdf下载0182-圆圆教程网
本书主要内容包括4部分:第一部分机械结构分析基础实验,包括机构及机械零件认知、平面机构运动简图的绘制、产品的机械结构分析、渐开线圆柱齿轮参数的测定、减速器拆 ... 於 xmj1688.com -
#51.機械工程系洪興林教授教師履歷 - 崑山科技大學
姓名:洪興林教授; 英文姓名:Horng, Thin-Lin; 學歷:成功大學土木研究所博士、國立交通大學機械工程碩士、淡江大學土木工程學士; 專長領域:機械結構力學分析 ... 於 web.ksu.edu.tw -
#52.精密機械結構分析_四技自控四甲等合開 - My數位學習
課程名稱, 精密機械結構分析_四技自控四甲等合開(10101, 10D31S01, 機械工程系, 四技車輛四乙). 閱讀權限, 不開放旁聽(僅成員可以閱讀). 課堂整理權限, 不開放. 於 120.117.3.21 -
#53.ANSYS 13.0机械与结构有限元分析从入门到精通: 胡仁喜,等
《ANSYS 13.0机械与结构有限元分析从入门到精通》以最新版本ANSYSl3.0为依据,对ANSYS分析的基本思路、操作步骤、应用技巧进行了详细介绍,并结合典型工程应用实例 ... 於 www.amazon.com -
#54.机械原理(2) - 机构的结构分析_唐大大鹏的博客
一,分析机构的组成:①,搞清楚机械的构造及运动情况;②,查明各构件和运动副的类别及位置。 二,选定视图平面. 三,取比例尺作图:①,先根据机械结构的 ... 於 blog.csdn.net -
#55.複材結構分析及材料測試| 國立陽明交通大學機械工程學系
計畫名稱, 複材結構分析及材料測試. 參與人, 蔡佳霖. 職稱/擔任之工作, 主持人. 計畫期間, 2013.05 ~ 2013.10. 補助/委託或合作機構, 財團法人工業技術研究院. 於 me.nycu.edu.tw -
#56.【機械結構分析軟體】Abaqus–全球頂尖的線性與非... +1
在這些機械、電子、能源、建築等諸多領域中,應用數值模擬已經成為了 ..., 第二個Inventor 框架分析, 這個功能必需搭配Inventor 框架產生器使用, 基本上專門對樑結構進行 ... 於 tag.todohealth.com -
#57.了得網工業技術_機械結構分析與設計實踐教程
《機械結構分析與設計實踐教程》(作者韋林、林泉)主要內容包括4部分,包括機械設計創意及綜合設計;機械傳動裝置的總體設計;常用減速器的類型、特點和結構;減速器 ... 於 www.liaode.com -
#58.機器人的結構分析,機器人機械結構設計的步驟,一文全面介紹_多源 ...
機器人的結構分析,機器人機械結構設計的步驟,一文全面介紹. 2021-07-01 由 一位工程師 發表於. (此處已添加圈子卡片,請到今日頭條客戶端查看). 機器人的結構 ... 於 dyfocus.com -
#59.机械工程中的有限元方法 - 新闻
有限元法是复杂机械结构设计中强度校核、性能分析和模拟、仿真的主要技术手段。从20 世纪50 年代在机械工程中开始应用以来,有限元法经历了60 余年 ... 於 new.qq.com -
#60.机械结构稳定性设计探讨_参考网
郎帅摘要:本文以机械结构的稳定性为研究对象,从设计方法的角度论述提高机械结构穩定性的措施。通过对机械结构稳定性影响因素的分析,探究机械稳定性 ... 於 m.fx361.com -
#61.36个机械结构原理动图,保证让你看懂这些机构!
36个机械结构原理动图,保证让你看懂这些机构!,仿真在线提供有限元分析代工代做服务、CAE有限元培训(ansys,abaqus,fluent,cfx,autofrom,Dynaform ... 於 www.1cae.com -
#62.機器人機械結構設計的步驟,一文全面介紹 - 資訊咖
機器人的結構分析,機器人機械結構設計的步驟,一文全面介紹. 2022年06月04日21:17 HKT. 機器人的結構分析,機器人機械結構設計的步驟,一文全面介紹. 熱門資訊. 於 inf.news -
#63.台大機械系-研究領域
組別, 研究方向, 研究領域. 固力組, 課程及研究領域包括結構分析與動力及破壞力學與波動力學、金屬成型實驗與分析電腦與週邊設備相關力學等,以提高系統可靠度,及達成 ... 於 140.112.16.109 -
#64.【書籍】機械設計原理與技術方法機械設計實用機構圖冊機構 ...
... 機構圖冊機構設計及應用圖例圖解機械結構設計要點分析及應用實例機械結露天拍賣就在露天拍賣,立即購買商品搶免運及優惠,還有許多相關商品提供瀏覽. 於 www.ruten.com.tw -
#65.【應用科學Aec】全新《ANSYS 14.5機械與結構分析實例詳解 ...
【新生活二手書店_應用科學Aec】全新《ANSYS 14.5機械與結構分析實例詳解》簡體ISBN:9787111480167│機械工業出版社│李萬全. 內容介紹本書通過大量典型實例, ... 於 shopee.tw -
#66.ANSYS結構分析師 - 產業學習網- 工業技術研究院
結構分析是確認設計物品質與安全性的必要手段,最常用的結構分析技術就是有限元素 ... 在從事精密機械、智慧機具、土木設計時的一個最佳化設計工具,結合結構分析與最 ... 於 college.itri.org.tw -
#67.Structure Design & Analysis 工具機結構設計與分析
工具機結構設計與分析. 講師:羅佐良博士. 工業技術研究院. 智慧機械科技中心. 課堂講義 ... 合理的結構設計,應該盡可能的提高共振頻率,意味著靜剛性的提高和. 於 140.120.25.41 -
#68.研討會/發表會-財團法人金屬工業研究發展中心
2015年機械結構分析應用技術研討會. 活動日期, 2015-04-01 ~ 2015-04-01. 場次. 活動地點, 高雄金屬中心研發大樓2F會議室. 主辦單位, 經濟部中小企業處(金屬中心協辦). 於 www.mirdc.org.tw -
#69.機械結構書| 飛比價格
機械結構 書價格推薦共596筆。另有機械結構設計技巧與禁忌、機械結構設計與工藝性分析、機械結構有限元分析。飛比為你即時比價,全台電商網購價格輕鬆找, ... 於 feebee.com.tw -
#70.結構分析| Creo,JetSoft 嘉航科技股份有限公司
為了解產品的效能、生命週期與可能故障模式,關鍵在於是否清楚產品的結構強度。機械負載、熱應力、螺栓張力、壓力條件與旋轉加速度等則是決定材料和設計強度需求的參考 ... 於 www.jetsoft-tech.com -
#71.機械設計原理實作心得(一) - 台大機械系電子報Vol.11, No1
... 與認識許多機械結構,對受力計算分析與設計機構更加了解並能用與之前截然不同的角度來看待機械,至此為大三的機械設計原理與往後實作奠下底子。 於 www.me.ntu.edu.tw -
#72.机械结构设计工程师需要什么样的分析软件? - 知乎专栏
机械 专业的学生,无论是在校的还是已经工作的,都经常为机械专业软件的多样性感到迷惑。我们身边有多少种机械专业软件啊,autocad, caxa, ug, ... 於 zhuanlan.zhihu.com -
#73.「機械結構設計」找工作職缺-2022年6月
... 銀行提供全台最多工作職缺,及專業求職服務,更多「機械結構設計」找工作職缺請上104人力銀行搜尋。 ... 機械設計分析研究員(肯學習無經驗可,不需輪班,不加班). 於 www.104.com.tw -
#74.机械结构分析与设计_百度百科
《机械结构分析与设计》是由北京理工大学出版社与2009年08月01日出版的一本机械行业书籍,作者李小红,韦林。 於 baike.baidu.com -
#75.使用ANSYS之機械結構動態分析__臺灣博碩士論文知識加值系統
中文摘要本研究探討工具機結構設計與結構剛性之特性。磨床結構與線馬磨床是由工作台、鞍座、軌道及底座構成。將次結構組合成整機,在整機分析時以有限元素法, ... 於 ndltd.ncl.edu.tw -
#76.PW2【電腦】機械結構有限元分析:ANSYS與 ... - 奇摩拍賣
PW2【電腦】機械結構有限元分析:ANSYS與ANSYS WORKBENCH工程應用@wa63695 | 如在購物上有什麼問題直接咨詢客服. 於 tw.bid.yahoo.com -
#77.機械件可靠度設計
物理分析法是從物品成功或失效的過程來討論可靠度問題,同樣有兩種方向:. 應力強度干涉模型,特別是在機械與結構可靠度領域中廣為應用。 隨機 ... 於 www.iem.yuntech.edu.tw -
#78.机械结构优化设计的应用及趋势探究 - ResearchGate
PDF | 机械结构设计是机械制造当中一个非常重要的环节,它的设计水平会对产品的质量产生直接影响。 ... 论文主要对机械机构优化设计的应用和发展的趋势进行了分析。 於 www.researchgate.net -
#79.工具機進給系統應用與結構分析技術
台灣精密工具機產業在整機與關鍵零組件硬體製造生產的實力已在國際上佔有一席之地,然而國產機台在設計創新上無法和歐美日廠商相比,仍有一大段差距。 於 www.pmc.org.tw -
#80.【圖解】工業機器人之五大機械結構及關鍵零組件分析|大和有 ...
【圖解】工業機器人之五大機械結構及關鍵零組件分析|大和有話說 ... 在射出成型機取出用機械手臂中,天行自動化(Alfa)與台灣精銳(Apex)為該領域 ... 於 meet.bnext.com.tw -
#81.平面機構的結構分析,如何計算自由度?如何繪製機構運動簡圖?
專欄中的這1000G資料涉及的範圍很廣,具體來說包括模具、機械加工、材料類、電氣行業、各種零件模型和非標等等領域,具體內容表現形式:文檔類(各類 ... 於 twgreatdaily.com -
#82.台灣邁達斯機械
NFX是集成CAE和CFD分析之有元素分析軟體,同時具備最佳化計算、拓樸設計和多體動力學 ... 結構用戶進行複雜的結構接觸計算、非線性計算、線性&非線性動態和疲勞分析, ... 於 www.midasuser.com.tw -
#83.國際主流結構分析軟體技術現狀剖析 - 壹讀
PATRAN已經被廣泛應用於航空、航天、汽車、船舶、鐵道、機械、製造業、電子、建築、土木、國防、生物力學等各個行業。 於 read01.com -
#84.台灣首枚衛星導航機(GPSR)機械外殼設計,分析與製造 - 洸碩科技
太空中心衛星導航機結構振動CAE分析,太空中心GPSR結構振動CAE分析,電腦輔助工程顧問服務,結構數值模擬顧問服務,CAE模擬顧問服務,結構分析顧問服務,熱流分析顧問服務 ... 於 cae-so.com -
#85.機械結構工程師工作職缺/工作機會-2022年7月
3. 熟練使用Pro/e(或Catia), AUTOCAD 等工程設計軟件,熟悉公差分析。 4. 熟悉常用塑膠,五金材料及加工成型工藝,能及時處理不良異常。 5. 熟悉塑膠及五金模具結構和 ... 於 www.1111.com.tw -
#86.五軸工具機載重件結構最佳化設計與分析
[1]其以機械結構. 設計分析的基本方程式推導與應用ANSYS 模擬之使用範例,其他有限元素分析法. 之相關慘考資料[2-5]。 翁嘉駿[6] 利用有限元素法及工具機結構設計觀念,提出 ... 於 ir.lib.ncut.edu.tw -
#87.觸控顯示器 - 政府研究資訊系統GRB
本計畫提出類紙式軟性觸控顯示器,藉由微奈米製程技術、顯示光學技術、軟性電子技術、機械結構分析技術及控制整合技術,彈性地發展整合軟性顯示、軟性多點觸控感測、 ... 於 www.grb.gov.tw -
#88.圖解機械結構設計要點分析及應用實例 - 博客來
本書結合機械設計的知識和方法,分析了機械結構的設計要點。圖解的機械結構主要包括螺紋連接、鍵連接、銷連接、帶傳動、鏈傳動、螺旋傳動、減速器、變速器、軸、聯軸 ... 於 www.books.com.tw -
#89.機械結構設計過程中應重點考慮哪些方面? - 百合問答
設計 · 1、理清主次、統籌兼顧。 · 2、在分析確定結構的同時,粗略估算結構件的主要尺寸並按一定的比例,通過繪製草圖,初定零部件的結構。 · 3、對初定的 ... 於 www.lilyans.com -
#90.有限元素法在含螺栓接點結構上的振動模擬分析
成,因此在使用有限元素法分析機械結構. 動態特性時,如何將螺栓扣件的動態特性. 成功的模擬出來是一件重要的課題。研究. 中將利用等效圓錐體的模型觀念,在螺栓. 於 www.artc.org.tw -
#91.好評再開班!工研院【智慧製造-機構設計與結構分析技術師 ...
工研院【機構設計與結構分析技術師】養成班,重點培訓電子產品兩大關鍵競爭力:設計與機電整合, ... 非相關領域,有志進入智慧製造及智慧機械設計及應用領域者。 於 www.accupass.com -
#92.LS-DYNA成功應用案例|鑫威資訊-機械土木結構分析,NVH分析
LS-DYNA 應用案例. 汽車工業. 被動式成員安全性分析. 機械結構分析. 車輛碰撞分析. 土木結構分析. 地震結構安全. 交通設施工程. 風力工程. 抗震材料研究. 航太工業. 於 www.simware.com.tw -
#93.固力組
CAD. 機械設計. 固力與破壞. 大 學 部. ME 2010. 電腦輔助機械製圖. ME3207. 電腦輔助設計概論. ME3218. 電腦輔助機構分析. ME 3210. 電腦輔助結構分析概論. 於 www.me.ntust.edu.tw -
#94.机械结构优化设计的应用与展望 - 论文网
机械结构 优化设计的思想和理论;优化方法;建模技术;结构分析技术;结构重分析技术;敏度分析技术;软件开发技术。机械结构优化设计的研究与开发主要集中在这几个 ... 於 m.lunwendata.com -
#95.Airiti Library華藝線上圖書館_機械眼結構分析與設計
本研究目的為創新球形超音波馬達結構設計,作為機械眼用。 ... 針對新型球體幾何結構進行設計分析,將機械眼轉動產生的偏心扭矩與自重及磁力產生預力,分別針對壓電材 ... 於 www.airitilibrary.com -
#96.機械設備原理動畫@ Ken's Blog :: 痞客邦::
如果不會動的結構沒有支持會動的機構,這個機動會變形,甚至嚴重損壞。為了避免這樣的情況,因此必須從力學的角度來分析機械各部會需要多少力才能動作 ... 於 www.kenddg.tw -
#97.模具產業培訓網- 進修課程/機械結構之設計模擬分析實務_8/25-26
課程大綱:, 精密機械設計原理、方法機械元件之應用機械元件破壞分析機械設計常見的結構問題. ANSYS Workbench結構模組功能及應用. CAD實體模型的匯入、定義材料性質等 ... 於 www.tmdia.org.tw -
#98.首頁/ 研究組別/ 固體力學組
在傳統機械工程領域中,固體力學可應用於機械設計,結構力學、結構可靠度、應力 ... 材料力學(二)、機械振動學、高等材料力學、有限元素法概論、應力分析、複合材料 ... 於 me.ncku.edu.tw